Steel Surface Inspection System
Traditional quality inspection involves manual checkpoints after the cooling bed. Inspectors must stop or slow down production to detect defects, which impacts efficiency. They focus on the steel coil surface, relying on experience to judge and record defects. Typically, they only record the guaranteed side, making it difficult to document both sides. Quality disputes arise because quality record cards are subjective and may not reflect true quality.
Improving steel coil quality focuses on surface defects, critical for applications in building materials, electronics, furniture, and transportation. Analysis shows that over 80% of secondary or defective products are due to surface issues like scratches, contamination, insufficient pickling, indentations, roll marks, and oil stains. Enhancing surface quality is vital for the market competitiveness of hot-rolled steel.
In the global market, competitive advantage comes from precise product quality and low prices. Automated inspection systems quickly and accurately identify, classify, remove, and record defects, giving production managers a complete view of surface quality. Higher yield rates and efficiency significantly boost the company's competitiveness.
Application
Steel Coil Surface Inspection
Detectable Defect Types
Mosquitoes, bubbles, holes, dents, contamination, gouges, scratches, creases, roll marks, zinc slag, etc.
Features
• High-resolution linear CCD for high-speed dynamic coil process inspection to increase yield.
• Line speed up to 1000 meters per minute.
• Abnormal images displayed with audio alerts or automatic label tagging.
• Inspection Accuracy 100μm
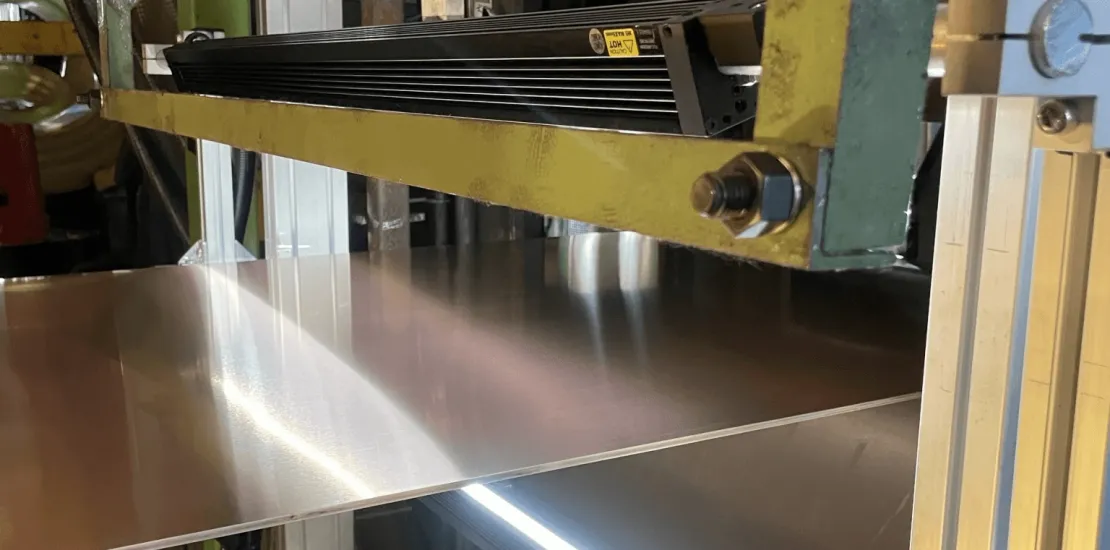
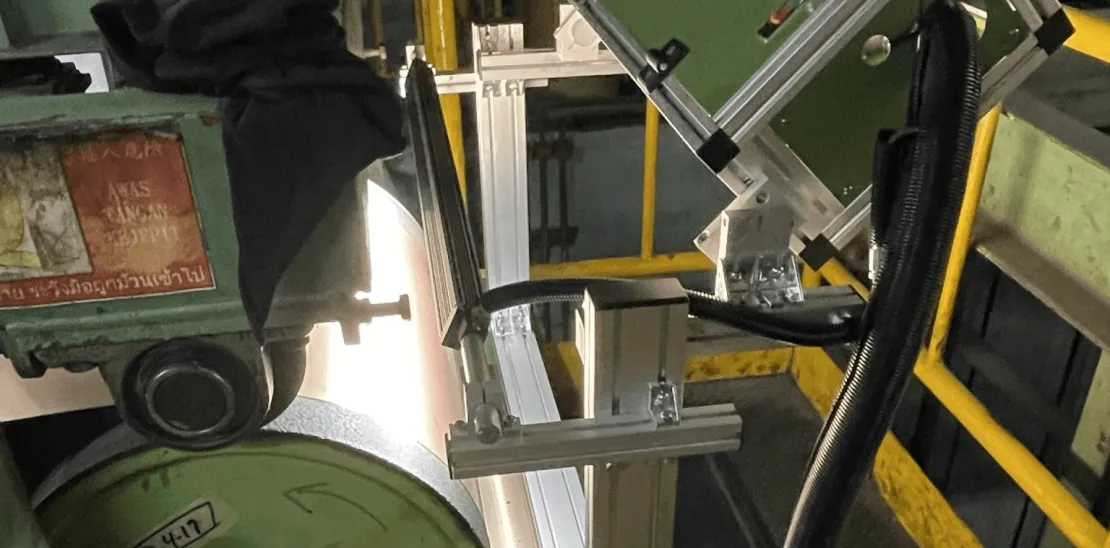
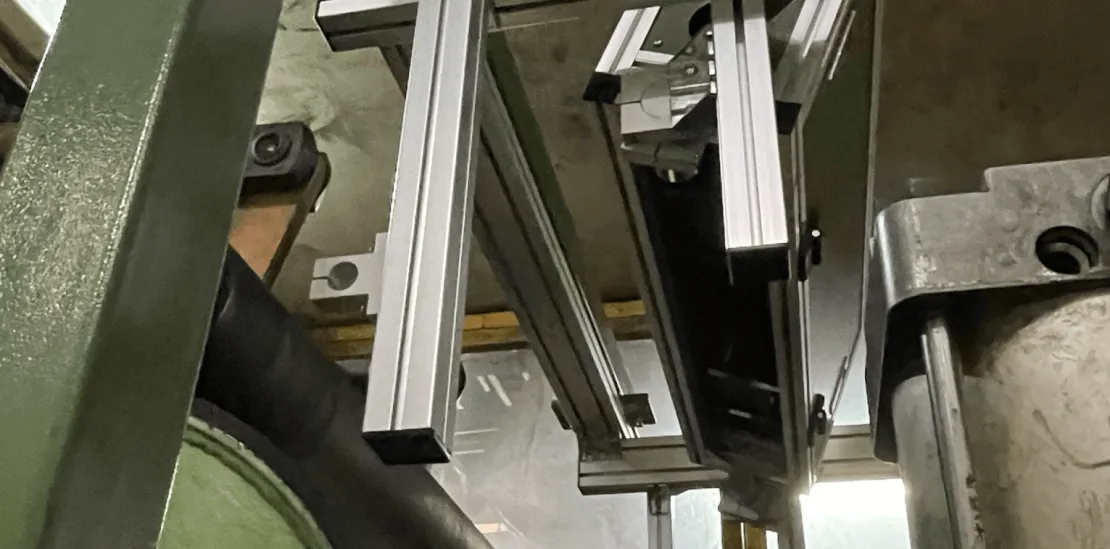
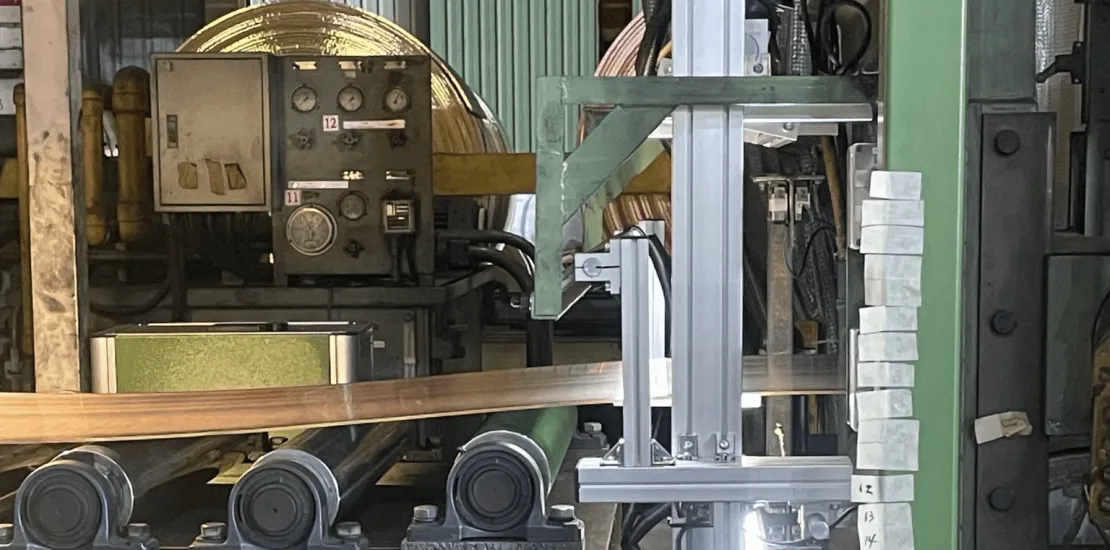
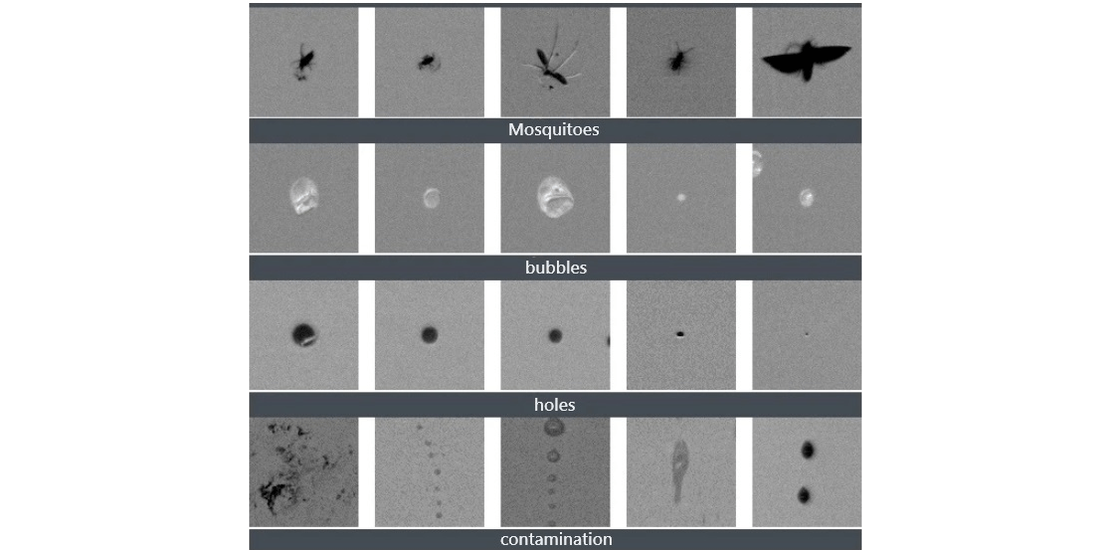
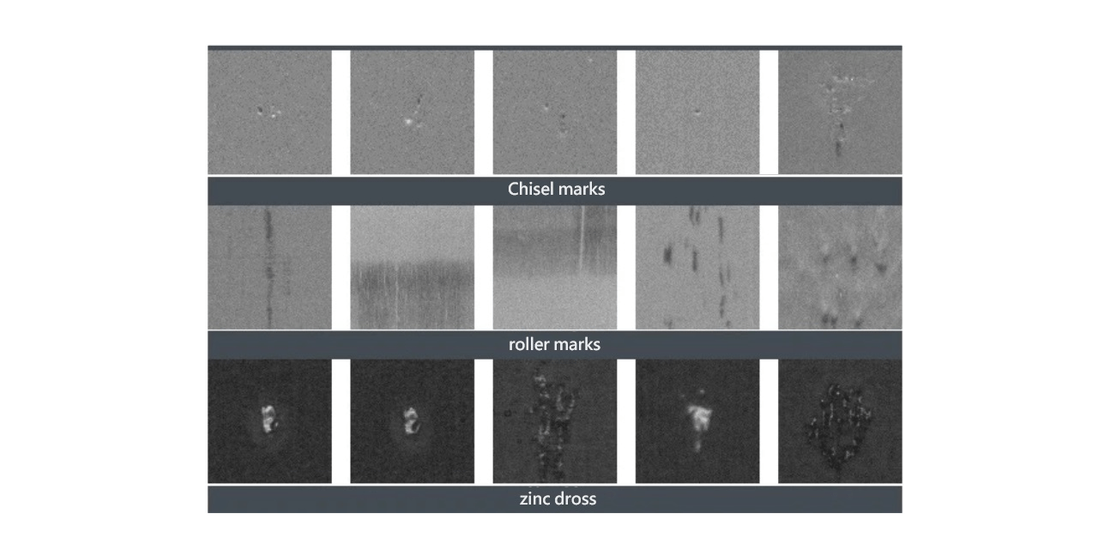
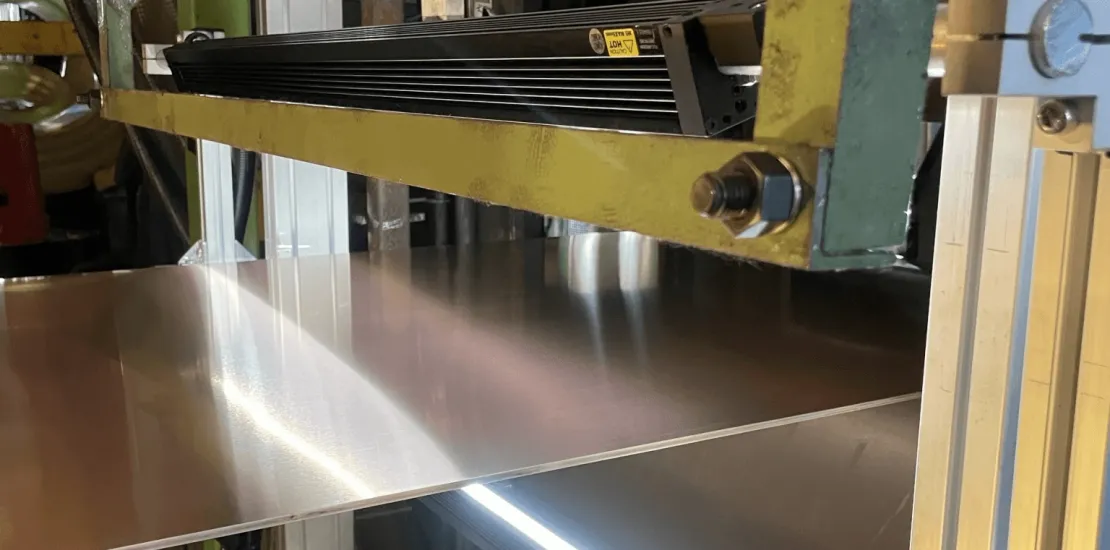
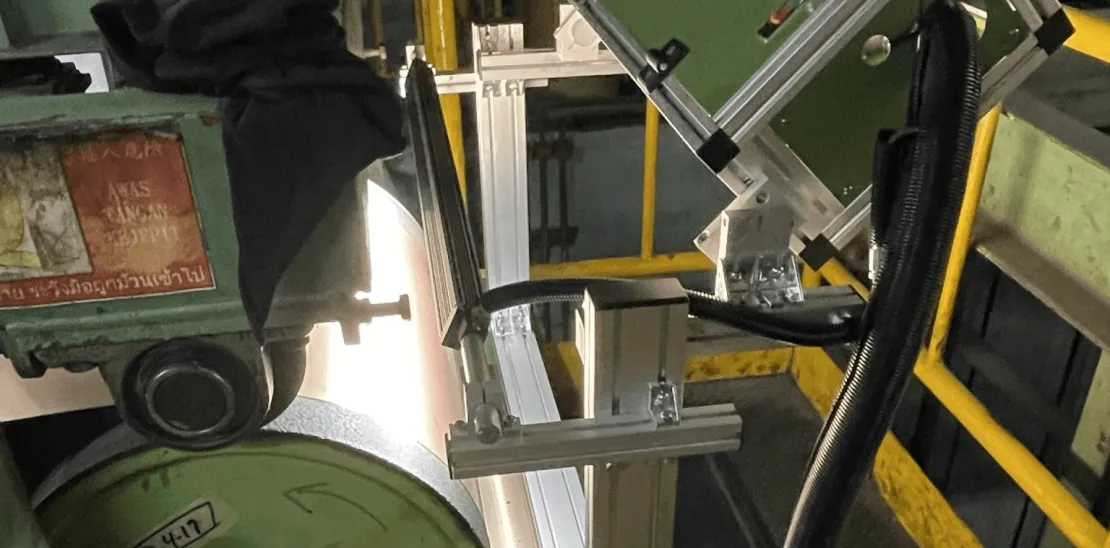
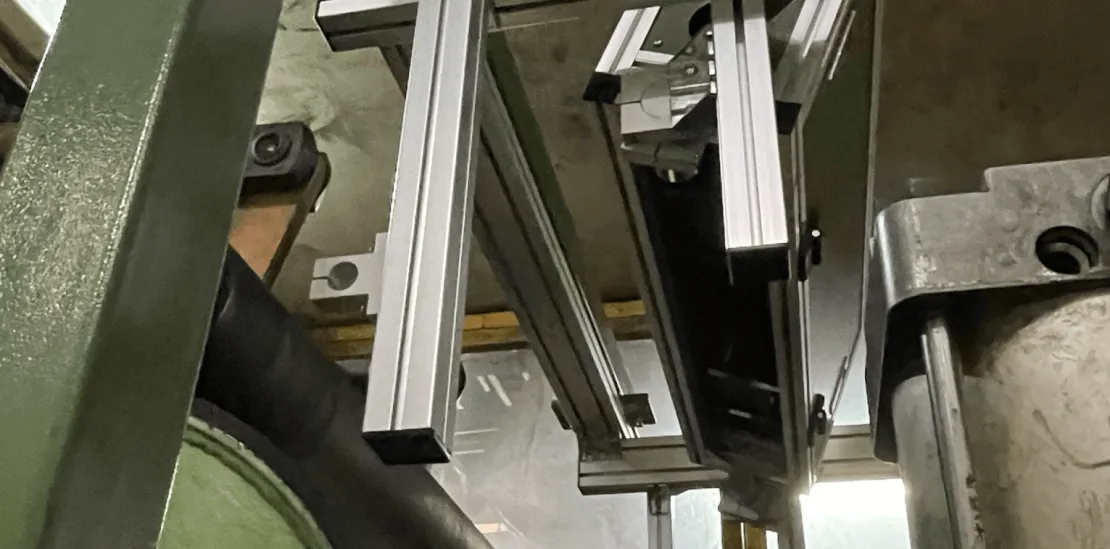
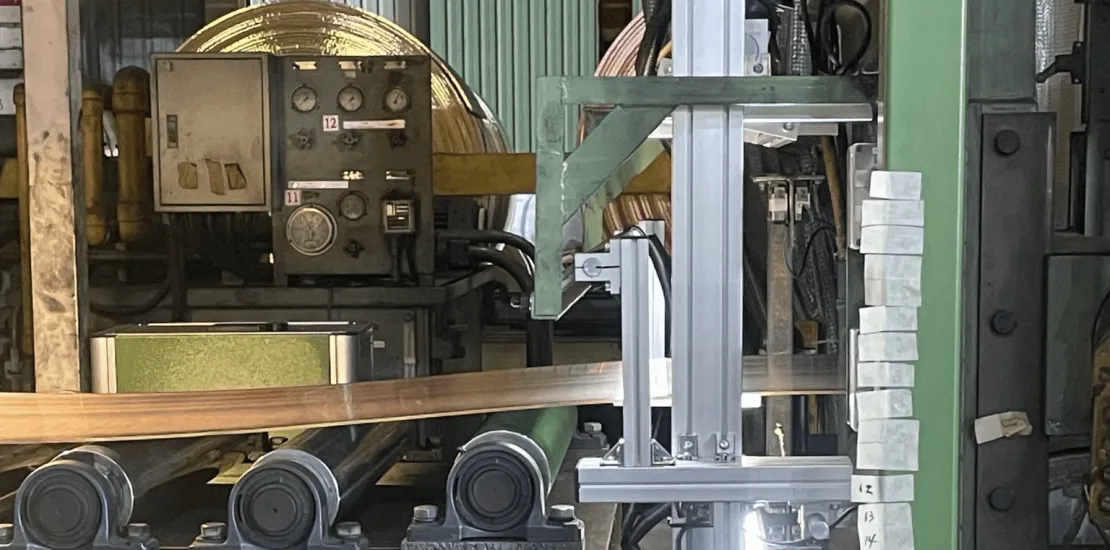
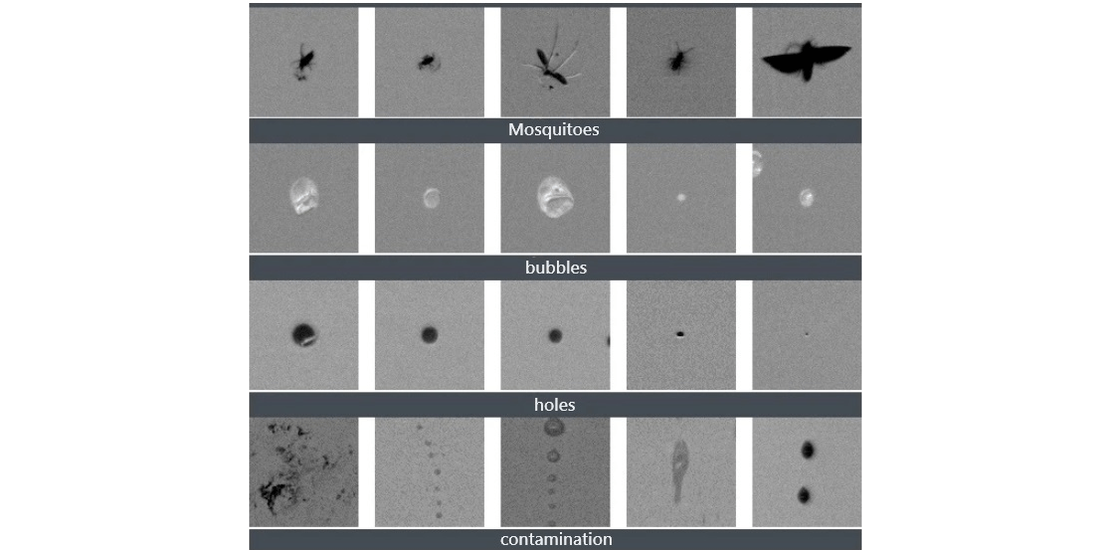
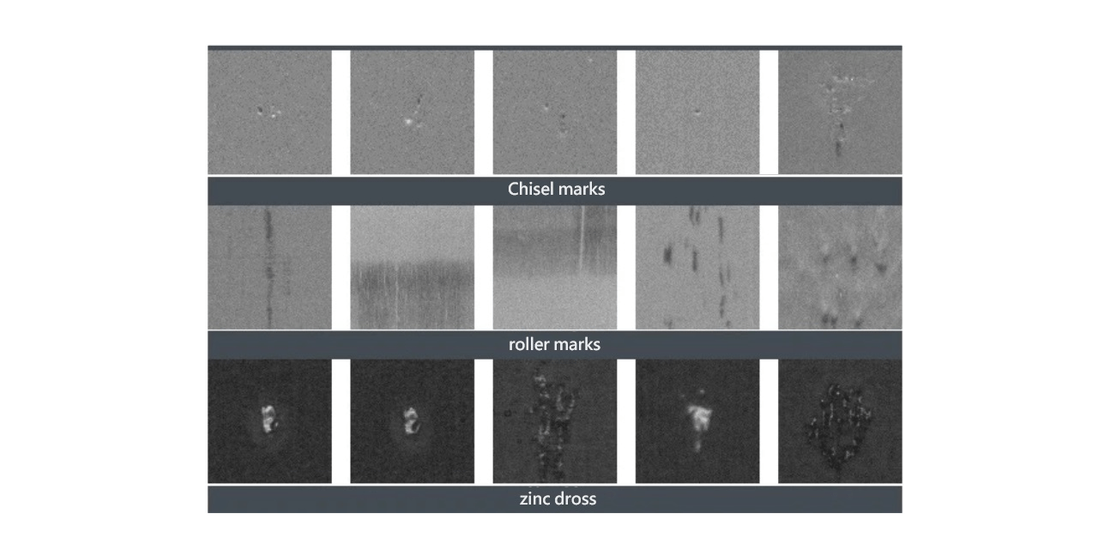
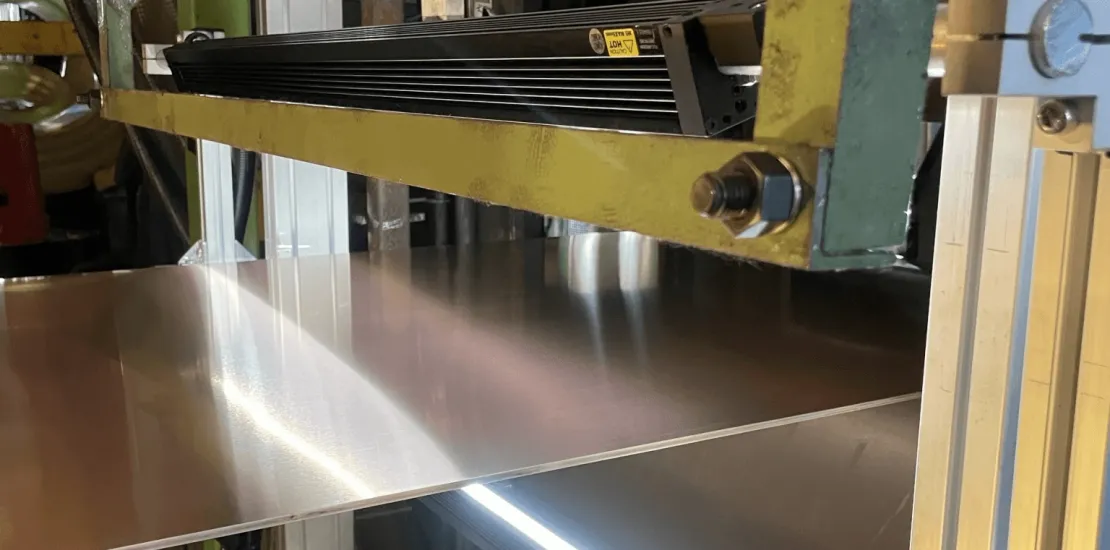
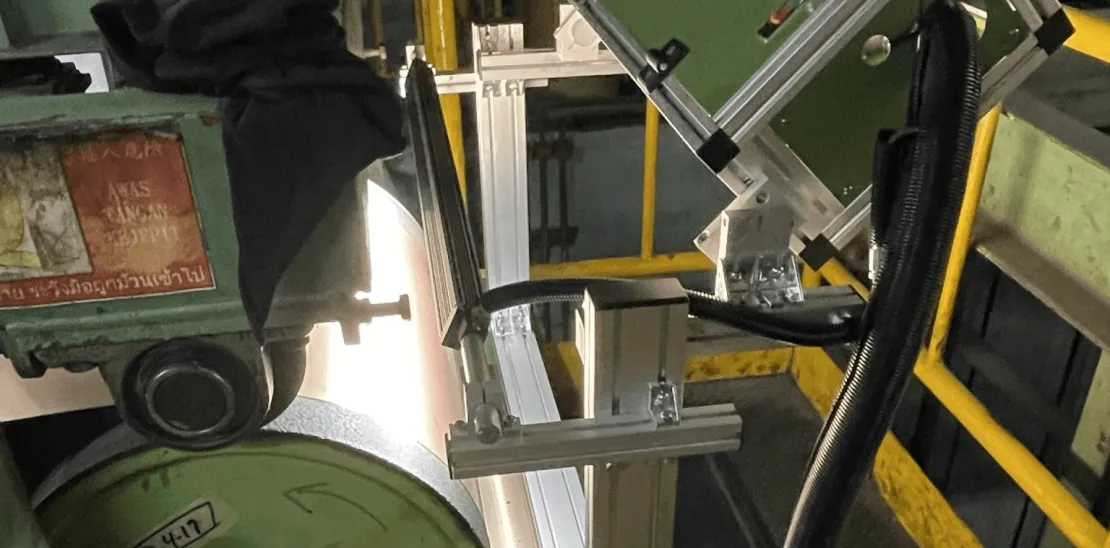
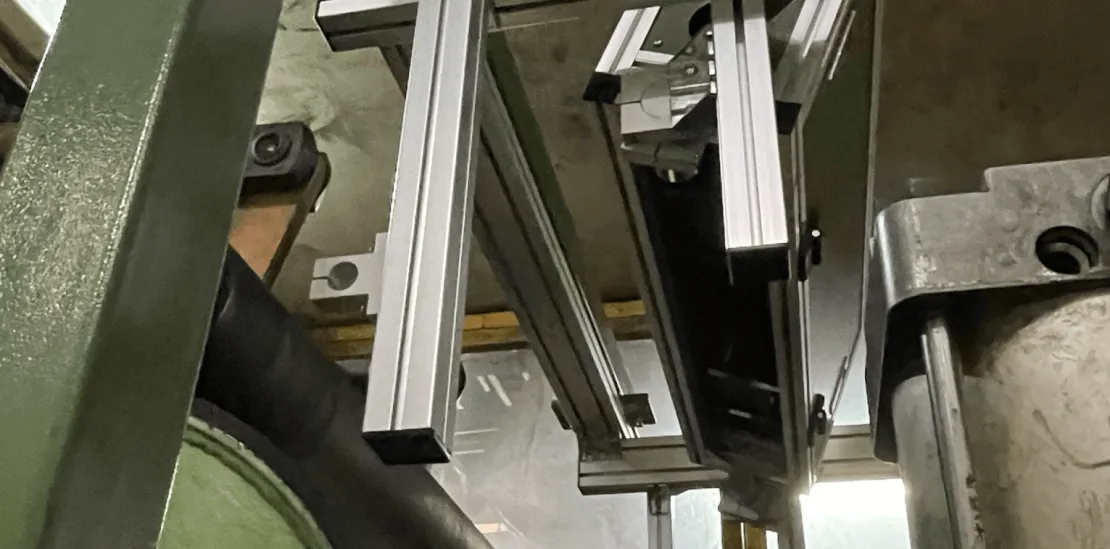
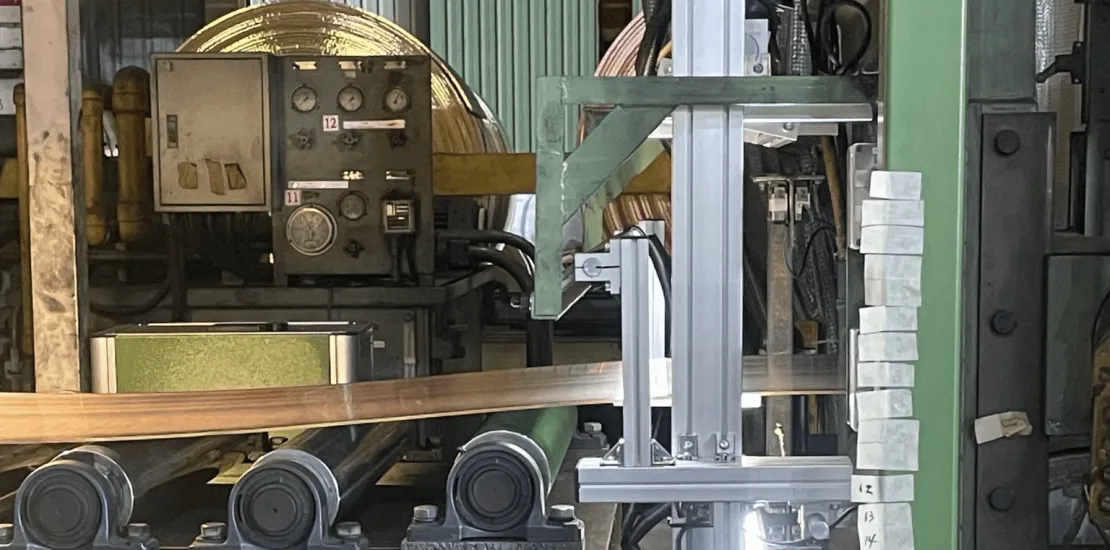
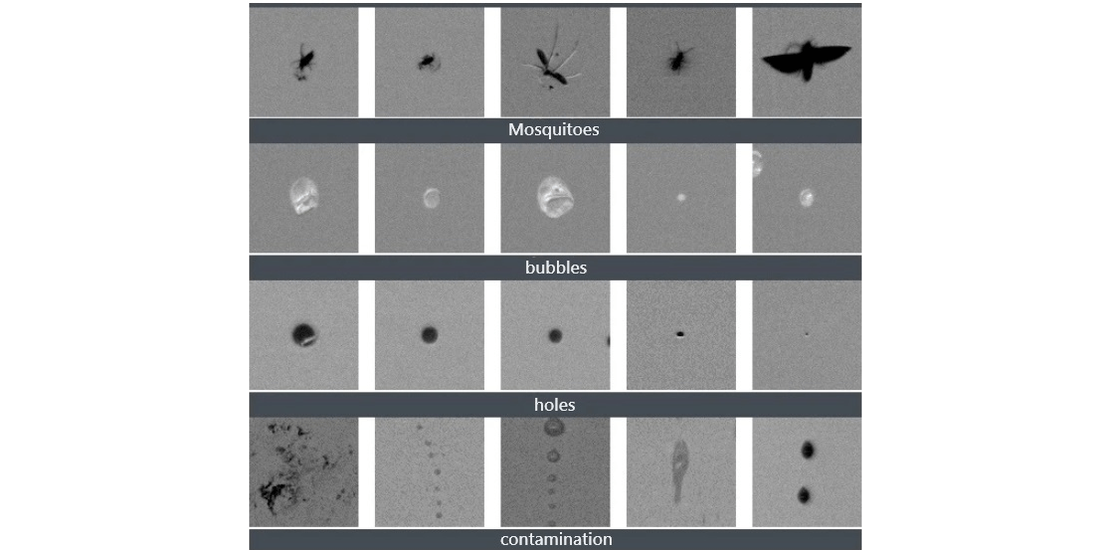
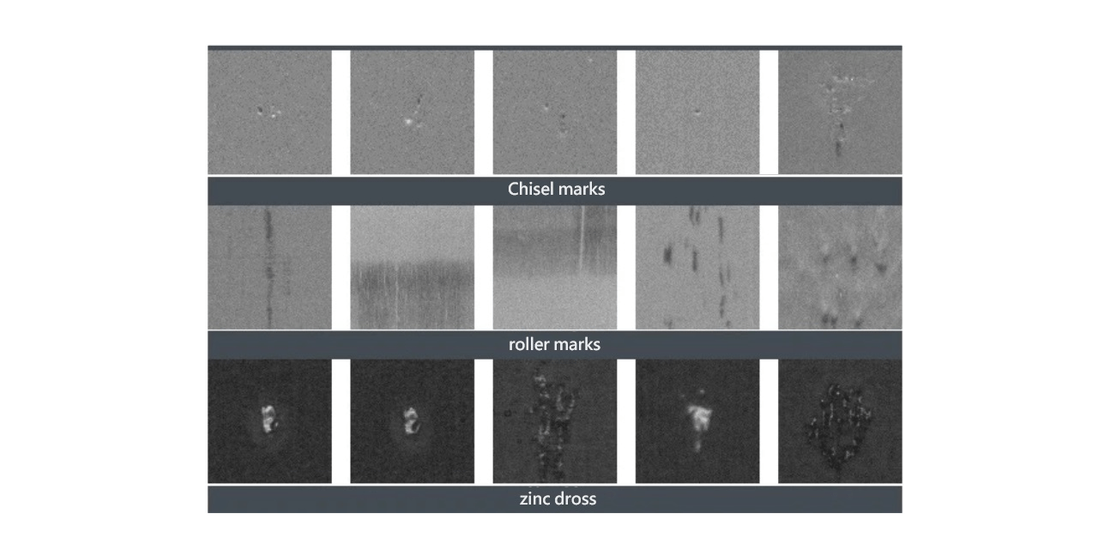
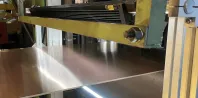
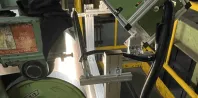
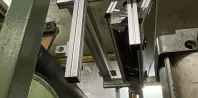
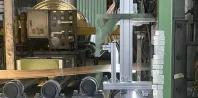
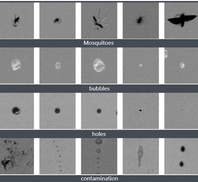
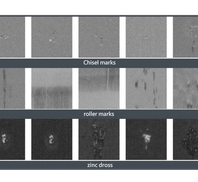